Preventing defects such as porosity or shrinkage in die-cast parts is crucial to ensuring the quality and integrity of the final product. Several measures are typically implemented to address these issues:
Optimized Process Parameters: Rigorous control of die casting parameters, such as metal temperature, injection pressure, and injection speed, is imperative. This involves continuous monitoring and adjustment to attain the precise conditions for filling the mold without introducing defects. For instance, a nuanced understanding of how variations in temperature affect material flow and solidification rates is essential for achieving optimal results.
Proper Mold Design: Mold design is a meticulous art. It goes beyond basic structure to encompass venting channels strategically placed to facilitate the escape of gases during filling, preventing porosity. Cooling channels are engineered with precision to regulate temperature differentials across the mold, ensuring uniform solidification and minimizing the likelihood of shrinkage. The devil is in the details when it comes to designing a mold that not only forms the desired part but does so with minimal defects.
Material Selection and Treatment: The choice of die-casting alloys is not arbitrary. It involves a thorough understanding of the material's characteristics and behavior under different conditions. Additionally, treatments such as degassing and desulfurization are not mere steps; they are strategic interventions to purify the molten metal, eliminating impurities and gases that could jeopardize the integrity of the final product. This level of scrutiny is indispensable for producing high-quality, defect-free parts.
Gate Design: Gate design isn't just about openings in the mold. It's about orchestrating the entry of molten metal with precision. Well-designed gates are a symphony of geometry that ensures a controlled, turbulence-free flow, distributing material evenly throughout the mold. This attention to detail is pivotal in preventing defects arising from uneven filling or turbulent flows that can compromise the integrity of the part.
Die Casting Machine Calibration: Calibration is not a routine check; it's a meticulous process that ensures die casting machines operate with the precision akin to a finely tuned instrument. Regular calibration and maintenance are paramount for upholding the machine's capability to apply pressure, temperature, and injection speed consistently. The meticulousness of this calibration directly correlates with the repeatability of the process, leaving no room for defects due to inconsistent application of forces.
Controlled Cooling Rates: Managing cooling rates isn't just about the passage of time; it's about orchestrating the gradual solidification of molten metal. This controlled cooling isn't a passive process; it's an active intervention to prevent rapid solidification that can result in internal stresses and defects like shrinkage. It involves a careful balance of time, temperature differentials, and the strategic placement of cooling channels in the mold.
In-Process Monitoring: Real-time monitoring isn't a passive observation; it's a proactive engagement with the die casting process. Sensors and feedback systems aren't mere observers; they are vigilant guardians, detecting deviations from set parameters and allowing for immediate adjustments. This dynamic monitoring isn't a luxury; it's a necessity to nip potential defects in the bud, ensuring that the production process stays on course without compromising on quality.
Use of Vacuum or Gas-Assist Techniques: The use of vacuum or gas-assist techniques isn't a casual choice; it's a strategic decision to actively remove air and gases from the mold cavity. This isn't just about extraction; it's about creating an environment within the mold that minimizes the presence of trapped gases, leaving no room for porosity. It's a meticulous process, ensuring that each casting is free from the defects that can compromise the part's functionality.
Civilian Die casting lightning parts-lignting cover
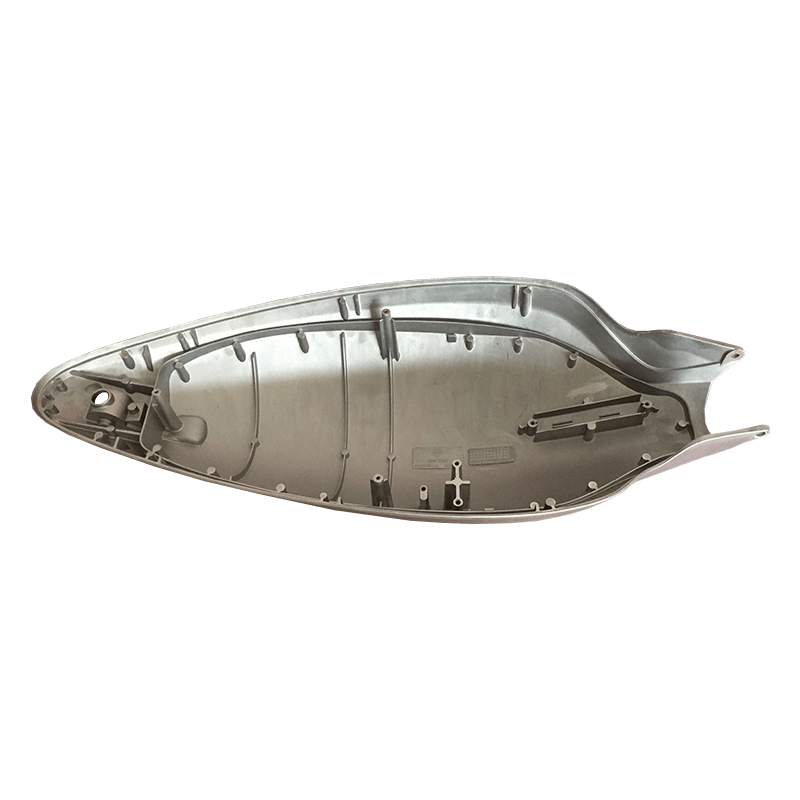
Civilian Die casting lightning parts-lignting cover
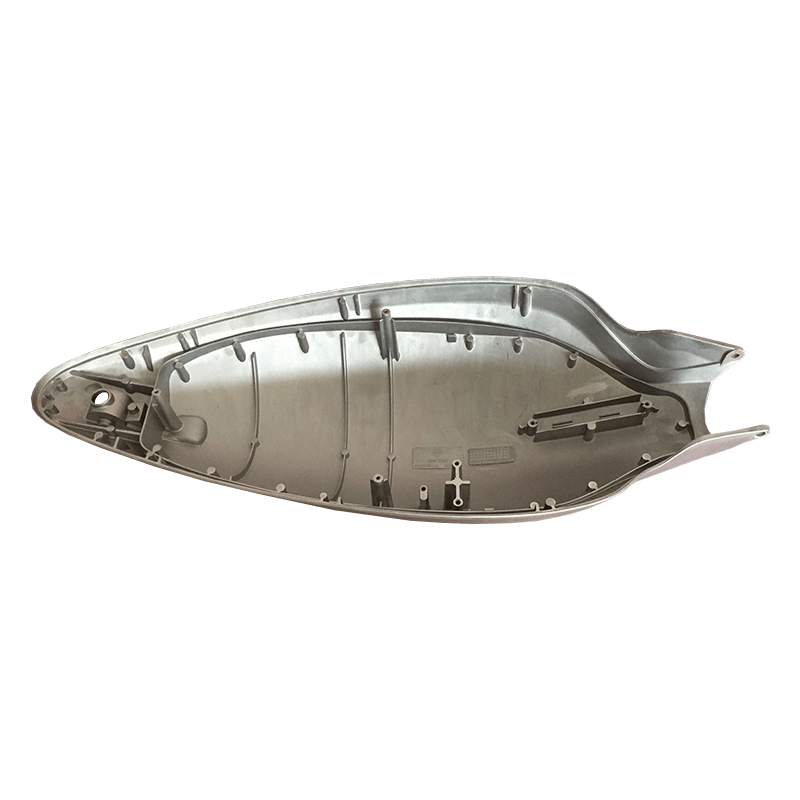