CNC machining is a manufacturing process that uses computer-automated machinery to create precision parts. In the context of auto parts, CNC machining is widely used to produce various components used in automobiles, including engine parts, transmission components, brake system parts, and much more.
Handling complex geometries and intricate designs in CNC machining auto parts requires a combination of advanced techniques, precision tools, and skilled expertise. Here are several methods commonly employed to handle such challenges:
1.Advanced CAD/CAM Software:
Employ state-of-the-art Computer-Aided Design (CAD) and Computer-Aided Manufacturing (CAM) software solutions. These tools offer sophisticated 3D modeling capabilities, enabling the creation of intricate part geometries. CAM software, in particular, assists in generating intricate toolpaths and simulations, ensuring precise machining of complex designs.
2.Multi-Axis Machining:
Invest in multi-axis CNC machining centers, including 4-axis and 5-axis machines. These machines provide enhanced flexibility by allowing simultaneous movement along multiple axes. By approaching the workpiece from various angles, intricate features can be machined accurately and efficiently.
3.Precision Tool Selection:
Select cutting tools tailored for complex geometries. High-quality end mills, ball mills, and tapered cutters with diverse cutting edges and angles are essential. These tools provide the precision necessary for intricate cuts and detailed features, ensuring the final product meets exact specifications.
4.High-Speed Machining (HSM):
Implement High-Speed Machining techniques to minimize cutting forces and vibrations. Reduced vibrations lead to improved surface finishes and enhanced accuracy, especially in intricate areas. HSM also prolongs tool life and maintains consistent quality throughout the machining process.
5.Optimized Toolpaths:
Develop optimized toolpaths using CAM software. Efficient toolpaths minimize unnecessary movements, reduce air cutting, and prevent tool wear. By streamlining the machining process, optimal toolpaths enhance productivity and precision, especially in intricate geometries.
6.Toolpath Strategies:
Utilize advanced toolpath strategies such as rest machining. Rest machining selectively targets areas where material remains after previous operations. This approach optimizes tool usage and prevents overcutting, ensuring intricate details are machined accurately.
7.Custom Fixturing:
Design custom fixtures and workholding solutions tailored to the specific intricacies of the auto part. Proper fixturing is critical for stability during machining. Custom fixtures prevent part movement and vibration, allowing for precise and intricate cuts without compromising accuracy.
8.Simulation and Prototyping:
Employ simulation software to visualize the entire machining process virtually. Simulations help identify potential issues and optimize toolpaths before actual production. Prototyping allows for physical testing of the machining process, ensuring that intricate features are machined correctly and meeting design specifications.
9.Quality Control:
Implement rigorous quality control protocols, including in-process inspections and measurements. Regular checks during the machining process ensure that intricate features meet specified tolerances and design requirements. Quality control measures guarantee the final auto parts conform to high-quality standards, meeting customer expectations.
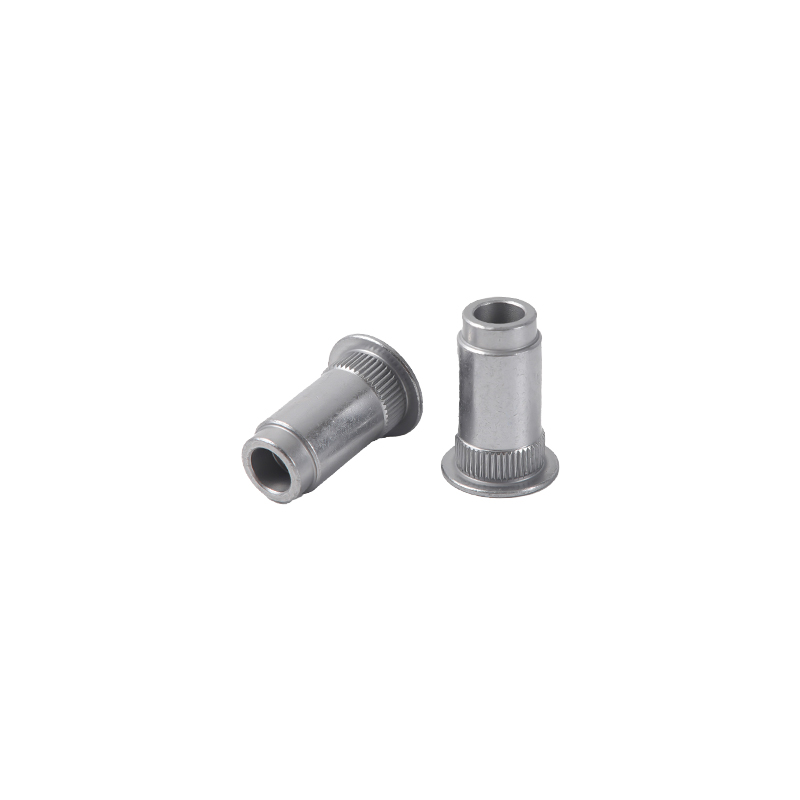
Application &Purpose: this part is accessary tensioner key component asslembled with pulley for heavy duty vehicle.
Material: Carbob steel 20#35#45#
Main Process: steel bar-hot forging-CNC machining-Zinc Nickel plating-packing