Solving issues associated with component distortion and warping in skinny-walled auto die casting components requires a cautious analysis of the basis reasons and implementation of appropriate measures at some point of the design, tooling, and production procedures. Here are a few strategies to deal with these troubles:
1.Optimize Design:
Work carefully with design engineers making use of computer-aided design (CAD) software and simulation gear to optimize the geometry of the skinny-walled component. Consider uniform wall thickness and right ribbing to decrease uneven cooling, that could lead to distortion. Conduct simulation analyses, which include finite detail analysis (FEA), to are expecting ability distortion problems and refine the layout iteratively.
2.Proper Tooling:
Invest in great die casting molds made from warmness-dealt with device metal. Proper venting, cooling channel design, and gating systems are critical. Venting permits for the escape of trapped gases, making sure uniform filling. Well-designed cooling channels facilitate controlled and even cooling in the course of the mold, lowering the likelihood of warping.
3.Controlled Cooling:
Implement controlled cooling tactics to keep away from rapid cooling differentials inside the element. Use superior mould temperature manage systems to regulate mildew temperature in the course of the casting cycle. This allows keep constant cloth properties and minimizes inner stresses, reducing the risk of distortion.
4.Material Selection:
Collaborate with cloth specialists to choose the right die casting alloy. Some alloys provide higher glide houses and minimum shrinkage, making them suitable for thin-walled elements. Consider elements inclusive of thermal conductivity and solidification characteristics to decrease the danger of warping during cooling.
5.Minimize Residual Stresses:
Control cooling costs to limit residual stresses within the part. Slow and managed cooling, particularly for the duration of the solidification section, helps reduce inner stresses. Properly designed cooling channels in the mould resource in achieving uniform cooling, thereby minimizing residual stresses and the ability for warping.
6.Process Optimization:
Continuously optimize the die casting technique parameters. Fine-tune injection velocity, pressure, and temperature based at the specific alloy and element geometry. Avoid abrupt adjustments in those parameters, that could cause turbulence and uneven filling. Consistent and controlled filling reduces inner stresses and minimizes distortion.
7.Heat Treatment:
Consider submit-casting warmth treatment procedures including stress relieving or annealing. These treatments assist stabilize the microstructure of the fabric, loosen up inner stresses, and reduce the chance of distortion. Consult with metallurgical professionals to decide the right warmth treatment method for the precise alloy used.
8.In-Process Monitoring:
Implement actual-time monitoring systems that use sensors to accumulate records in the course of the casting technique. Analyze this data to hit upon versions and deviations right away. With real-time insights, changes can be made to the method parameters, ensuring that any troubles contributing to distortion are addressed at once.
9.Post-Casting Machining:
Design the thin-walled component with allowances for post-casting machining. Machining critical dimensions after casting permits for correction of any distortion that would have passed off. Utilize precision machining strategies and tools to attain the specified tolerances and dimensions, ensuring the very last component meets specifications.
10.Continuous Improvement:
Establish a systematic method to continuous improvement. Analyze production data, such as times of distortion and their reasons. Implement corrective and preventive actions based on facts-driven insights. Encourage pass-useful collaboration between design, engineering, and production teams to discover and address capacity troubles early in the product development procedure. Regularly review and update quality practices based on instructions discovered from preceding initiatives to further beautify the producing method and limit distortion in skinny-walled car die casting components.
Auto Die casting parts-Ermission Exhaust bracket
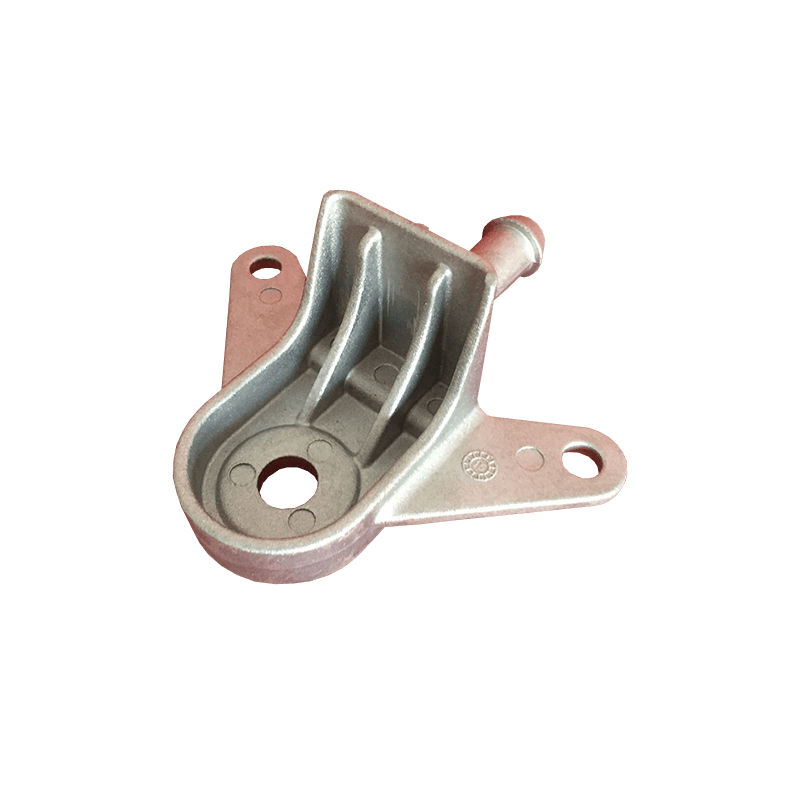
Auto Die casting parts-Ermission Exhaust bracket
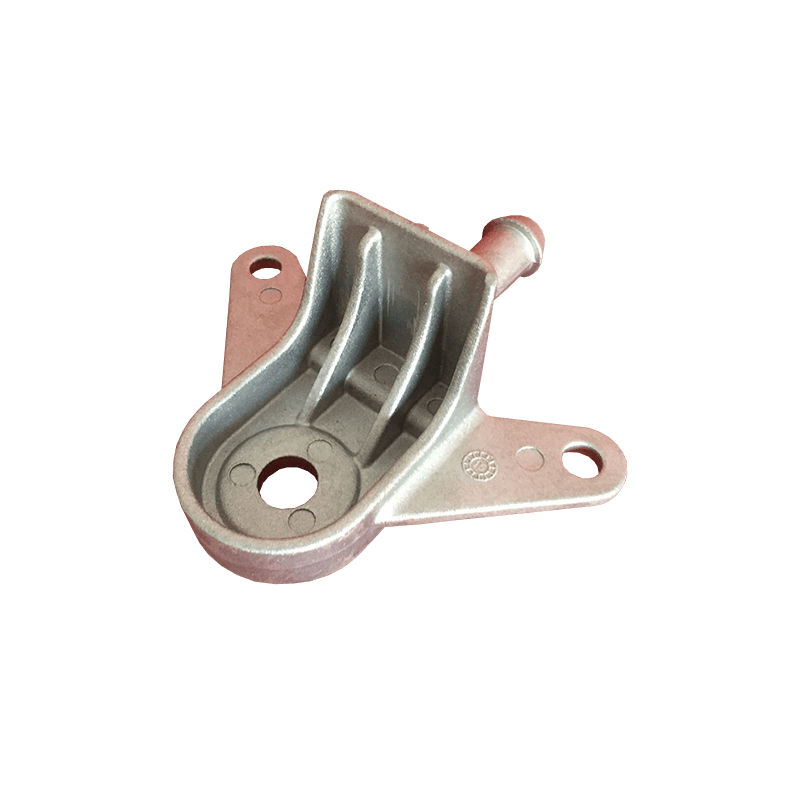